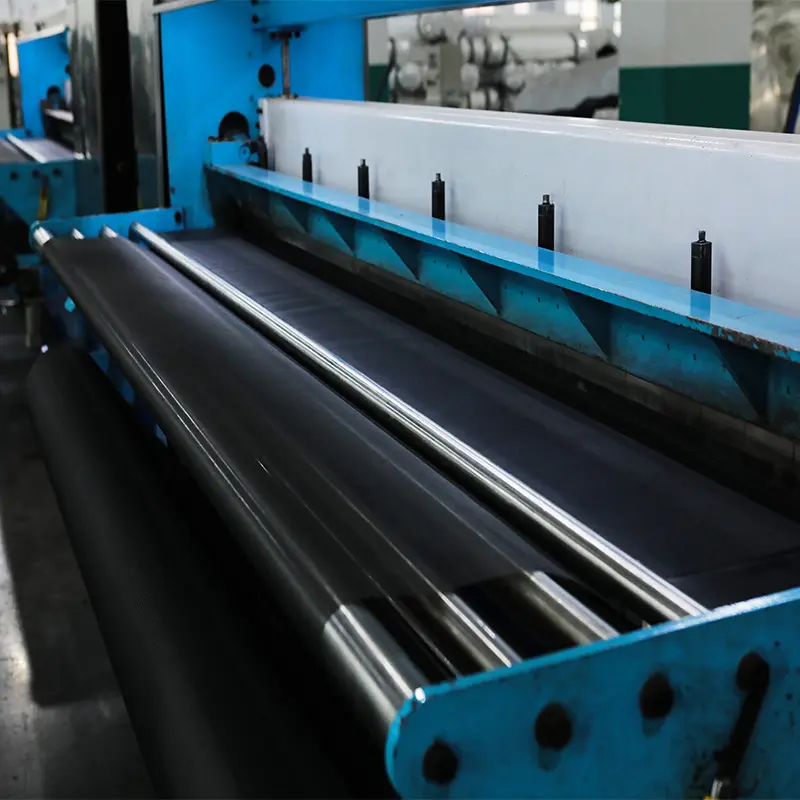
1. Fabric Feeding
Fabric Preparation
- First, the mesh or other lightweight fabric to be pleated is prepared. The fabric usually needs pre-treatment, such as cleaning and drying.
Feeding System
- The fabric is fed into the machine through a feeding system. This can be a conveyor belt, rollers, or other types of feeding mechanisms to ensure smooth movement of the fabric within the machine.
2. Pleat Formation
The formation of pleats typically relies on mechanical devices and some physical principles:
Mechanical Devices
- Pleating Rollers: Some pleating machines use one or more pairs of pleating rollers that rotate to fold the fabric. The surface of these rollers is often designed with specific patterns or grooves to create pleats.
- Pleating Plates: Another common pleating device is pleating plates, which can be moved or adjusted to change the fabric’s folding pattern, thus creating different types of pleats.
- Pneumatic Devices: Some advanced pleating machines use air flow to control the pleating of the fabric. Pneumatic devices push and pull the fabric into specific positions using blowing and suction methods, thereby forming pleats.
Folding and Pleating
- Stretching and Folding: The fabric passes through specific mechanical devices (such as pleating rollers or plates), which apply force to fold the fabric in designated areas, creating pleats. The depth and spacing of the pleats can be controlled by adjusting the settings of the devices.
- Multiple Layers of Pleats: In some pleating machines, the fabric may pass through multiple pleating devices to create complex pleat patterns or multiple layers of pleats.
3. Pleat Fixing
To ensure the pleats are durable, many pleating machines are equipped with pleat-fixing devices:
Heating Devices
- Some pleating machines include heating devices that fix the pleats through hot air or heating plates. Heating helps to set the pleats in place, preventing them from flattening out during subsequent use.
Cooling Systems
- After heating, some pleating machines have cooling systems to quickly cool the fabric and set the pleat shape.
4. Fabric Output
Discharge System
- The pleated fabric is then discharged through the machine’s output system. This can be a conveyor belt, roll, or other mechanisms to ensure the fabric exits the machine while retaining the pleat effect.
Finishing and Inspection
- After discharge, the fabric typically undergoes finishing and inspection to ensure the pleat effect meets the required standards, with any necessary adjustments or corrections made.
5. Control System
Modern mesh pleating machines are often equipped with electronic control systems that allow operators to:
Set Pleat Parameters
- Such as pleat depth, width, and spacing.
Monitor Operation Status
- Real-time monitoring of the machine’s operation, including fabric feed speed and pleat quality.
Adjust Operations
- Make necessary adjustments to ensure consistency and quality of the pleat effect.
Through these steps and components, a mesh pleating machine effectively creates uniform, durable pleats on fabric. These principles and technologies may vary slightly depending on the machine model and manufacturer, but the overall workflow remains consistent.